Products >> Iron >>
Cast iron pump parts
In the realm of manufacturing cast iron pump parts, the journey from molten metal to reliable component is a delicate ballet of artistry and precision. Two standout techniques, sand casting and lost foam casting, each bring their own unique strengths and challenges. Today, we’ll explore the defects that can arise in these processes, how to detect and avoid them, and innovative methods to enhance surface quality.
Understanding the Defects: What Can Go Wrong?
Even the most skilled craftsmen face challenges. Defects in cast iron pump parts can manifest in various forms, jeopardizing performance and reliability. Here are some common culprits:
-
Porosity: Tiny voids or bubbles within the metal can form due to trapped gases during solidification, compromising structural integrity.
-
Shrinkage Cavities: As molten iron cools, it contracts. If the material doesn't have enough feed to compensate for this shrinkage, cavities may form, especially in thicker sections.
-
Inclusions: Foreign materials, such as sand or slag, can become trapped in the casting, leading to weaknesses.
-
Surface Roughness: Imperfections on the surface, whether from the mold or cooling processes, can impact the efficiency and aesthetics of pump parts.
-
Misalignment: Variations in mold assembly or pouring techniques can lead to misaligned features, affecting the fit and function of pump components.
Detecting Defects: The Eyes and Ears of Quality Control
To safeguard against defects, robust detection methods are essential. Here’s how to ensure quality:
-
Visual Inspection: The first line of defense. Skilled technicians examine the surface for visible flaws, roughness, or signs of inclusions. A keen eye can catch many issues early.
-
Non-Destructive Testing (NDT): Techniques such as ultrasonic testing, radiography, and magnetic particle inspection allow for internal examination without damaging the part. These methods help identify porosity and internal defects.
-
Dimensional Analysis: Using coordinate measuring machines (CMMs) to ensure that each part adheres to precise specifications. Deviations can indicate potential misalignment or shrinkage issues.
-
Metallurgical Analysis: Examining microstructures through microscopy to detect defects at a microscopic level. This process can reveal the effects of poor casting techniques or materials.
Avoiding Defects: Proactive Strategies
Preventing defects is as crucial as detecting them. Here’s how to minimize the risk:
-
Optimize Mold Design: For both sand and lost foam casting, a well-designed mold with appropriate gating and venting systems can greatly reduce porosity and shrinkage. Ensuring the flow of molten iron is unobstructed promotes even filling and minimizes trapped gases.
-
Temperature Control: Maintaining optimal pouring temperatures is vital. Too hot can lead to oxidation; too cool can cause flow issues. Using thermal analysis can help optimize these parameters.
-
Alloy Composition: Selecting the right alloy can also play a significant role. Adjusting the carbon and silicon content can enhance fluidity and reduce the risk of defects.
-
Quality Sand: In sand casting, using high-quality, well-graded sand reduces the chances of inclusions and surface defects. Regular testing and recycling of sand can maintain its quality.
-
Careful Foam Patterns: In lost foam casting, ensuring the quality of foam patterns is key. Imperfections in the foam can translate into defects in the final casting. Investing in high-quality patterns can prevent many issues.
Enhancing Surface Quality: The Finishing Touch
A smooth surface isn’t just about looks; it enhances performance. Here are effective methods to promote surface quality:
-
Surface Treatments: Techniques such as shot blasting or vibratory finishing can remove imperfections and improve surface finish. These methods help prepare the part for any additional coatings or treatments.
-
Coatings: Applying protective coatings can not only enhance aesthetics but also provide corrosion resistance, essential for pump parts exposed to harsh environments.
-
Machining: For parts requiring a high degree of precision, post-casting machining can achieve the desired surface finish. This step is particularly effective in ensuring tight tolerances.
-
Heat Treatment: Post-casting heat treatment can help relieve stresses and refine the microstructure, leading to improved surface characteristics and overall performance.
In the dynamic world of cast iron pump parts, sand casting and lost foam casting present unique challenges and opportunities. By understanding potential defects and implementing robust detection and prevention strategies, we can uphold the highest quality standards.
Embracing innovative practices not only enhances product reliability but also solidifies our reputation for excellence. Every flawless part we produce reflects our commitment to quality and continuous improvement.
Ready to elevate your projects? Contact us today to discover how we can help you achieve outstanding results in cast iron pump parts! Let’s transform challenges into opportunities and set new benchmarks for casting excellence.
Products Category
Contact Us
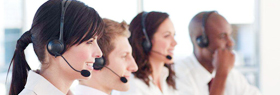
E-mail: [email protected]
WeChat: 18332109035
Whatsapp: 18332109035
Add: Shi Jiazhuang, He Bei Province