Coated Sand Casting vs Resin Sand Casting
Many people often confuse coated sand casting and resin sand casting due to their similar names and the fact that both utilize sand to form molds. Although both methods are part of the broader sand casting family, they differ significantly in terms of material, technique, surface finish, and the types of parts they can produce. In this article, we’ll break down the key differences between coated sand casting and resin sand casting, helping you understand when and why to choose one method over the other.
At Shata Castings, we specialize in both coated sand casting and resin sand casting, offering tailored solutions to meet your specific needs. Whether you're looking for high-precision components or large-volume industrial parts, we have the expertise to deliver top-quality castings.
1. What is Coated Sand Casting?
Coated sand casting, also referred to as shell molding or lost shell casting, involves creating a mold by applying a fine, heat-resistant coating over a sand pattern. This process provides a smooth, durable shell, improving surface finish and dimensional accuracy compared to traditional sand casting methods.
Key Steps in Coated Sand Casting:
- Pattern Creation: The mold is formed using a sand pattern, typically combined with a binder.
- Coating Application: A fine, heat-resistant material, such as silica sand or zircon, is applied to the sand pattern, forming a smooth coating.
- Drying and Firing: The coated mold is dried and heated to solidify the shell and create a durable, precise mold.
- Metal Pouring: Molten metal is poured into the shell, filling the mold cavity and forming the desired casting.
- Cooling and Removal: Once the metal cools, the shell is removed, leaving behind the final casting.
Advantages of Coated Sand Casting:
- Superior Surface Finish: The coating helps produce a much smoother surface compared to uncoated sand molds, reducing surface roughness.
- High Dimensional Accuracy: Coated sand casting offers tight tolerances and precise details, reducing the need for additional finishing.
- Excellent Detail Reproduction: This method captures intricate designs and sharp details, making it ideal for complex components.
- Reduced Porosity: The shell structure minimizes defects like porosity, resulting in stronger and more durable castings.
Best Applications for Coated Sand Casting:
- Aerospace components
- Automotive parts requiring precision
- Electronics and medical devices with intricate designs
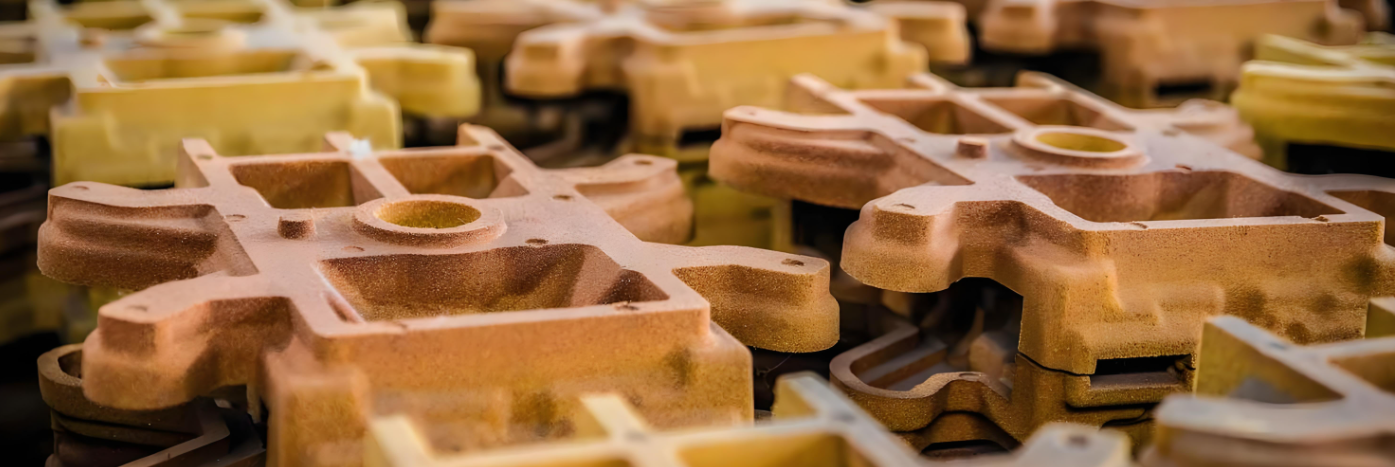
2. What is Resin Sand Casting?
Resin sand casting (or resin-bonded sand casting) uses a mixture of sand and a resin binder to form a mold. Unlike coated sand casting, this method does not require a fine coating. Instead, the sand itself is bonded using a resin that hardens quickly, making it a cost-effective method for casting large-volume, medium-to-large parts.
Key Steps in Resin Sand Casting:
- Sand Mixture Preparation: Sand is combined with a resin binder (such as phenolic or furan resins) to form a moldable mixture.
- Mold Formation: The resin-bonded sand is packed around a pattern to create a mold cavity.
- Hardening: The mold hardens through air-drying or baking in an oven.
- Metal Pouring: Molten metal is poured into the hardened mold cavity, solidifying into the desired part.
- Breakout: Once the metal cools, the sand mold is broken away to reveal the final casting.
Advantages of Resin Sand Casting:
- Cost-Effective: Resin sand casting is typically more affordable than coated sand casting due to the simpler molding process.
- Faster Setup: Resin molds set quickly, allowing for faster production and reduced lead times.
- Versatile: This method works well for a wide range of metals, including ferrous and non-ferrous alloys.
- High Productivity: Ideal for medium-to-large-scale production runs, particularly for industrial and automotive components.
Best Applications for Resin Sand Casting:
- High-volume industrial parts, such as engine blocks and machinery components
- Heavy-duty components like piping, valves, and construction parts
- Automotive and construction equipment
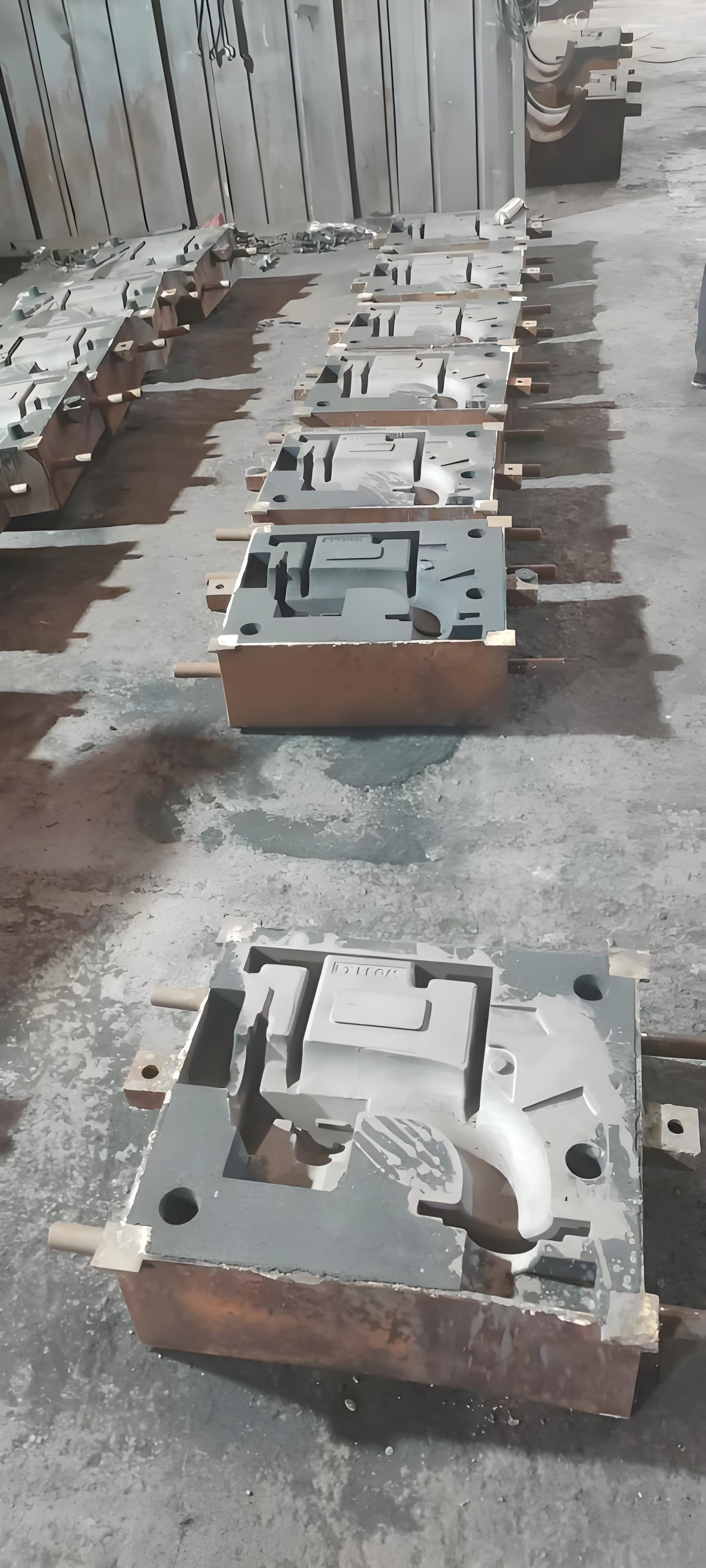
Key Differences Between Coated Sand Casting and Resin Sand Casting
While both methods fall under the sand casting umbrella, they have key differences that impact their surface quality, part size, production speed, and overall cost. Here’s a breakdown:
Feature | Coated Sand Casting | Resin Sand Casting |
---|---|---|
Mold Material | Fine sand coated with a heat-resistant shell | Sand mixed with resin binder |
Surface Finish | Smoother, finer surface with reduced roughness | Rougher surface, may require additional finishing |
Dimensional Accuracy | High precision with tight tolerances | Moderate accuracy, less fine detail |
Detail Reproduction | Excellent, captures intricate patterns and details | Good, but may not capture fine details as effectively |
Post-Processing | Less post-processing needed | Often requires additional finishing to smooth surfaces |
Production Speed | Slower due to coating and drying time | Faster, as resin molds set quickly |
Cost | More expensive due to the coating process | More affordable, suitable for large-volume production |
Applications | Aerospace, automotive, high-precision components | High-volume industrial and automotive parts |
Part Size | Ideal for small to medium-sized parts | Can accommodate larger parts, including heavy-duty industrial components |
Ideal for | Complex, high-precision, or low-volume parts | High-volume, larger industrial parts, and simple designs |
Part Size Comparison: Coated Sand Casting vs Resin Sand Casting
Coated Sand Casting:
- Best for Small to Medium Parts: Ideal for producing small to medium-sized parts that require high precision. It is often used for complex components in industries like aerospace and automotive.
Resin Sand Casting:
- Ideal for Larger Parts: This method is better suited for producing larger, heavier components, such as engine blocks, machine parts, and construction equipment. Resin sand casting is ideal for high-volume manufacturing and can handle parts with larger dimensions.
Which Method Should You Choose?
The decision to use coated sand casting or resin sand casting depends on several factors, such as the part size, surface finish, production speed, and budget.
-
Choose Coated Sand Casting if:
- You need high precision and fine surface finishes.
- The components require intricate designs or tight tolerances.
- You are producing parts for industries like aerospace, automotive, or electronics that require superior quality and detail.
-
Choose Resin Sand Casting if:
- You are looking for faster production and cost-effective casting solutions for larger parts.
- You are working on high-volume industrial production, such as engine blocks, piping, and machinery components.
- Surface finish is less of a priority, and you need to produce large parts quickly.
Finding the Perfect Sand Casting Solution for Your Project with Shata Castings
While coated sand casting and resin sand casting both utilize sand molds, they are suited for different casting needs. Coated sand casting is the go-to method for high-precision, small-to-medium parts that require fine detail and a smooth surface finish, making it ideal for industries such as aerospace and automotive. On the other hand, resin sand casting offers a more cost-effective and fast solution for larger, high-volume castings, especially in industries that prioritize production speed and large parts.
At Shata Castings, we specialize in both coated sand casting and resin sand casting, offering expert solutions tailored to your project’s requirements. Contact us today to discuss your casting needs and get started on your next project!
FAQ
Contact Us
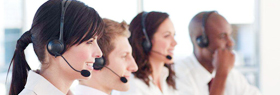
E-mail: [email protected]
WeChat: 18332109035
Whatsapp: 18332109035
Add: Shi Jiazhuang, He Bei Province