Products >> Aluminium
Aluminum casting is one of the most efficient and cost-effective ways to create lightweight, durable, and high-precision components for a wide range of industries. Whether you're looking to manufacture custom aluminum parts, aluminum die castings, or high-quality cast components for your next project, this process can provide the strength, flexibility, and cost savings you need.
In this guide, we’ll cover everything you need to know about aluminum casting, including the different casting methods, the advantages of using aluminum, and how to choose the best casting technique for your specific needs.
If you're searching for a reliable aluminum casting supplier for your business, keep reading to find out why aluminum casting should be your go-to solution!
Why Choose Aluminum Casting?
Aluminum casting offers multiple advantages that make it an excellent choice for various manufacturing needs:
- Lightweight and Durable: Aluminum parts are significantly lighter than steel and other metals, making them ideal for industries like automotive, aerospace, and electronics.
- Corrosion Resistance: Aluminum’s natural oxide coating makes it resistant to rust and corrosion, even in harsh environments.
- Cost-Effective: Aluminum is widely available and affordable, reducing production costs, especially when used in high-volume runs.
- Versatility: Aluminum can be cast into complex shapes, making it suitable for both simple and intricate designs.
These benefits make aluminum casting a top choice for businesses looking to produce precision-engineered parts while keeping costs low and quality high.
Types of Aluminum Casting Processes
The aluminum casting process can be done in several ways depending on your needs. Here are the most common methods we use:
1. Die Casting
For high-volume production of aluminum parts with complex shapes, die casting is an ideal solution. This method uses high pressure to inject molten aluminum into a mold, producing parts with fine details and tight tolerances. Die casting is commonly used in the automotive, electronics, and consumer goods industries.
2. Sand Casting
Sand casting is a flexible and affordable method for creating large or low-volume aluminum parts. The process involves packing sand around a pattern to create a mold, which is then filled with molten aluminum. It’s perfect for applications such as engine blocks, pumps, and valves.
3. Investment Casting (Lost Wax)
For highly detailed and intricate aluminum parts, investment casting offers unmatched precision. This method is often used in industries such as aerospace, medical, and defense for parts that require high performance and fine features.
4. Permanent Mold Casting
This process involves pouring molten aluminum into reusable molds, allowing for high-quality parts with smooth surfaces and stronger material properties. It is often used for medium-volume runs and is ideal for components that require high mechanical strength, such as brackets and housings.
5. Gravity Die Casting
Gravity die casting uses the force of gravity to fill the mold with molten aluminum, making it ideal for medium to large aluminum parts that require good mechanical properties.
Applications of Aluminum Casting
Aluminum casting is used in a variety of industries, and its versatility makes it ideal for many applications. Some of the most common industries and parts include:
- Automotive: Aluminum castings are used for engine blocks, transmission cases, wheels, and chassis components. The lightweight nature of aluminum helps reduce vehicle weight, improving fuel efficiency and performance.
- Aerospace: In aerospace, aluminum casting is used to produce turbine blades, engine components, and aircraft frames that must meet high-performance standards.
- Electronics: Aluminum castings are used for heat sinks, housings, and enclosures due to the material’s excellent thermal conductivity.
- Industrial Equipment: Components like pumps, valves, and gearboxes are frequently cast in aluminum for durability and resistance to wear.
- Marine: Aluminum castings are corrosion-resistant, making them perfect for marine engines, boat hulls, and outdoor fixtures.
Whether you need aluminum parts for heavy machinery or lightweight consumer products, the casting process provides endless possibilities for creating high-quality, customized components.
Why Work with Us? The Advantage of Choosing Our Aluminum Casting Services
As a leading aluminum casting supplier, we specialize in producing custom aluminum castings that meet your exact specifications. Here’s why you should consider partnering with us:
- Expertise: Our team of skilled engineers and casting specialists have years of experience producing high-quality aluminum parts.
- Advanced Equipment: We invest in the latest casting technologies, including automated die-casting machines, especially high locking-force, such as 1250T, 1600T, 2000T, 3000T, and advanced CNC machining to ensure the highest standards of precision and quality. Our state-of-the-art equipment allows us to handle even the most complex projects with speed and accuracy, delivering consistent results on every order.
- Quality Assurance: We follow rigorous quality control measures at every step of the process to ensure your aluminum castings meet or exceed industry standards. From the initial pattern creation to final finishing, we conduct thorough inspections to ensure defect-free parts.
- Cost-Effective Solutions: We offer competitive pricing for both small and large orders, making us a great choice for low-volume and high-volume casting needs.
- On-Time Delivery: We understand the importance of deadlines and ensure that all orders are completed on time, every time.
- Global Reach: Located in China, we offer cost-effective aluminum casting services for customers worldwide.
Ready to get started? Contact us today for a free quote on your next aluminum casting project. Our team is ready to help you with all your casting needs.
Products Category
Contact Us
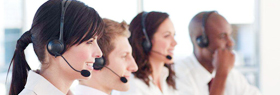
E-mail: [email protected]
WeChat: 18332109035
Whatsapp: 18332109035
Add: Shi Jiazhuang, He Bei Province