Products >> Aluminium >>
Automotive die castings
Apllication of Automotive Die Castings
-
Engine Components
- Engine Blocks: Houses the engine's cylinders and internal components.
- Cylinder Heads: Covers the engine block, containing valves and combustion chambers.
- Oil Pans: Collects and stores engine oil.
-
Transmission Parts
- Transmission Cases: Enclosures that house transmission components for automatic and manual systems.
- Shifter Housings: Supports gear shifting mechanisms.
-
Suspension and Chassis
- Control Arms: Connect the suspension system to the vehicle's frame.
- Knuckles: Support wheel bearings and connect suspension to steering components.
-
Powertrain Components
- Differential Housings: Encase the gears that allow for wheel speed differences during turns.
- Flywheels: Store rotational energy and smooth power delivery.
-
Body and Interior Parts
- Door Handles: Provide functional and aesthetic features for vehicle doors.
- Trim Components: Enhance the vehicle's interior appearance.
Advantages of Die Casting in Automotive Manufacturing
-
Precision and Accuracy:Die casting allows for the creation of complex shapes with tight tolerances, ensuring that components fit together perfectly in assembly.
-
Lightweight: Reduces overall vehicle weight, contributing to improved fuel efficiency and performance.
-
Strength and Durability: Die-cast parts can withstand high stresses, making them suitable for demanding automotive environments.
-
Excellent Surface Finish: Die-cast parts typically have a smooth surface finish, reducing the need for additional machining or finishing processes, which saves time and costs.
Common Materials Used
- Aluminum Alloys:
A356: Excellent corrosion resistance (ASTM, EN).
AlSi9Cu3: Widely used in Europe (EN).
ADC12: Popular in Japan (JIS).
- Aluminum Alloys:
Manufacturing Process
- Mold Creation: Molds are designed based on specific part requirements.
- Melting: The metal is melted and prepared for casting.
- Die Casting: The molten metal is injected into the mold under high pressure.
- Cooling and Solidification: Parts cool quickly in the mold, allowing for rapid production cycles.
- Finishing: Post-casting processes include machining, surface treatments, and quality inspections.
Automotive die castings play a crucial role in the efficiency, performance, and durability of vehicles, supporting the industry's ongoing advancements in technology and sustainability.
Products Category
Contact Us
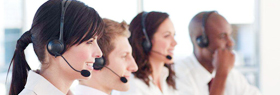
E-mail: [email protected]
WeChat: 18332109035
Whatsapp: 18332109035
Add: Shi Jiazhuang, He Bei Province