Forgings
Drop down menu or left navigation bar to our specific forging products
As a leading forging supplier in China, we take pride in producing high-quality forged components tailored to the diverse needs of our clients. Understanding the various forging methods is essential. It helps in selecting the right approach for your specific applications. In this article, we’ll explore key forging techniques, including precision forging, and highlight what sets our company apart in the industry.
What is Forging?
Forging is a manufacturing process that shapes metal by applying compressive forces, resulting in components that exhibit enhanced strength, durability, and structural integrity. Key forging methods include die forging, drop forging, open die forging, and precision forging, each offering unique advantages depending on the application.
Types of Forging Processes
-
Closed Die Forging: Also known as die forging, this process utilizes precision-shaped dies to create components with exact dimensions. It’s ideal for high-volume production and is widely used for manufacturing parts like gears and crankshafts.
-
Drop Forging: This technique involves dropping a hammer onto heated metal, quickly deforming it into the desired shape. Drop forging is highly efficient for creating intricate designs and is commonly used for critical parts such as connecting rods and automotive components.
-
Open Die Forging: In open die forging, flat or simple dies are used to shape larger workpieces, such as shafts, rings, and blocks. This method offers design flexibility but often requires additional machining to achieve final specifications. It’s particularly suited for low-volume production or custom parts.
-
Hammer Forging: This process employs a hammer to apply rapid force to the metal, enabling quick shaping. Hammer forging can be used in both open and closed die applications, making it versatile for various manufacturing needs.
-
Precision Forging: A more advanced form of forging, precision forging achieves tighter tolerances and superior surface finishes. This method minimizes material waste and can produce complex geometries, making it ideal for applications where exact specifications are crucial.
-
Custom Forging: We specialize in providing custom forging solutions tailored to your specific requirements. Whether you need unique shapes, sizes, or materials, our engineering team collaborates with you to deliver exactly what you need.
The Forging Process
Our forging process is designed for efficiency and quality, encompassing several key steps:
-
Heating: The metal is heated to an optimal temperature to enhance its malleability, preparing it for shaping.
-
Shaping: Using advanced machinery, the heated metal is formed according to the chosen method—whether it’s drop forging, precision forging, or open die forging.
-
Cooling: After shaping, the forged metal undergoes controlled cooling, critical for achieving desired mechanical properties and minimizing residual stresses.
-
Finishing: Finally, we perform precision machining and surface treatments as needed to meet your exact specifications.
Why Choose Us?
As one of the top forging companies in China, we combine cutting-edge technology with decades of industry experience. Our commitment to quality ensures that every piece we produce meets stringent standards. From drop-forged components to intricate precision forgings, we’re equipped to handle projects of any scale.
By partnering with us, you benefit from:
- Expertise: Our skilled engineers are dedicated to finding the best forging solutions tailored to your needs.
- Quality Assurance: We implement rigorous quality control measures throughout the manufacturing process.
- Innovation: Continuous investment in technology enhances our capabilities and efficiency.
FAQs About Forging
1. What is the main advantage of forging over other manufacturing processes?
Forging produces components with superior mechanical properties, such as increased strength and durability, compared to parts made through processes like casting or machining.
2. What materials can be forged?
Commonly forged materials include steel, aluminum, titanium, and other alloys. The choice of material often depends on the intended application and required properties.
3. How do I determine which forging process is best for my project?
Choosing the right forging process depends on factors such as part size, complexity, production volume, and material specifications. Our engineering team can help you evaluate your options.
4. Can you provide custom forged components?
Yes, we specialize in custom forging solutions tailored to your specific requirements, including unique shapes, sizes, and materials.
5. What industries do you serve?
We serve a variety of industries, including automotive, aerospace, construction, and energy, providing high-quality forged components for numerous applications.
Understanding the various forging processes—such as die forging, drop forging, open die forging, and precision forging—is crucial for making informed decisions in metal manufacturing. At Shata, we are committed to delivering exceptional forging solutions that meet your unique requirements.
Let us help you forge a successful path with high-quality, reliable components tailored to your specifications.
Contact Us
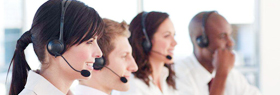
E-mail: [email protected]
WeChat: 18332109035
Whatsapp: 18332109035
Add: Shi Jiazhuang, He Bei Province