Which is the Best Sand Casting Method?
When selecting the optimal sand casting method for gray and ductile iron, a critical question arises: Which method provides the best balance of surface quality, production cost, and pattern cost?
Understanding these factors is crucial for decision-makers to make informed choices.
Choosing the best sand casting method for gray and ductile iron involves balancing surface quality, production costs, and tolerance. Whether you need the superior finishes of Coated Sand Casting, the precision of Resin Sand Casting, or the economy of Green Sand Casting, we have the right solution for you.
Contact us at Shata Castings today to discuss your casting needs and let us help you achieve your project goals!
Understanding these factors is crucial for decision-makers to make informed choices.
1. Sand Casting Methods For Gray And Ductile Iron
1.1 Coated Sand Casting
Coated sand casting involves using sand that is coated with a resin binder. The sand is shaped around a pattern, and heat is applied to cure the resin, creating a strong, detailed mold. This method enhances surface finish and dimensional accuracy, making it suitable for complex geometries
1.2. Resin Sand Casting
Resin sand casting utilizes chemically bonded sand mixed with a resin. Patterns are formed, and the mixture is packed around them. Once cured, the mold is ready for pouring molten metal. This method provides excellent surface finishes and tight tolerances, ideal for precision components.
1.3. Green Sand Casting
Green sand casting uses a mixture of clay, sand, and water as a binder. Patterns are pressed into the damp sand to create molds. This traditional process is cost-effective and allows for good surface quality, though it may require machining for tighter tolerances.
1.4. Vertical Sand Molding
Vertical sand molding involves packing sand vertically around a pattern in a two-part mold. This automated process enhances mold strength and consistency, allowing for efficient production of high-quality castings with good surface finishes and moderate tolerances.
1.5. Lost Foam Sand Casting
Lost foam sand casting uses foam patterns that are coated and then surrounded by sand. When molten metal is poured in, the foam vaporizes, leaving behind the desired shape. This method offers good surface finishes and allows for complex designs but can be more expensive due to the intricate pattern-making process.
Coated sand casting involves using sand that is coated with a resin binder. The sand is shaped around a pattern, and heat is applied to cure the resin, creating a strong, detailed mold. This method enhances surface finish and dimensional accuracy, making it suitable for complex geometries
1.2. Resin Sand Casting
Resin sand casting utilizes chemically bonded sand mixed with a resin. Patterns are formed, and the mixture is packed around them. Once cured, the mold is ready for pouring molten metal. This method provides excellent surface finishes and tight tolerances, ideal for precision components.
1.3. Green Sand Casting
Green sand casting uses a mixture of clay, sand, and water as a binder. Patterns are pressed into the damp sand to create molds. This traditional process is cost-effective and allows for good surface quality, though it may require machining for tighter tolerances.
1.4. Vertical Sand Molding
Vertical sand molding involves packing sand vertically around a pattern in a two-part mold. This automated process enhances mold strength and consistency, allowing for efficient production of high-quality castings with good surface finishes and moderate tolerances.
1.5. Lost Foam Sand Casting
Lost foam sand casting uses foam patterns that are coated and then surrounded by sand. When molten metal is poured in, the foam vaporizes, leaving behind the desired shape. This method offers good surface finishes and allows for complex designs but can be more expensive due to the intricate pattern-making process.
2. Rank According To Surface Quality, Production Costs, and Tolerances
2.1. Surface Quality((Highest to Lowest)
Coated Sand Casting: Best surface finish, surface roughness ranges from 6.3 μm Ra to 12.5 μm Ra (25 μm Rz to 50 μm Rz). Coated sand casting offers a superior surface finish compared to resin sand casting. The coating process involves applying a fine layer of material to the sand, which helps in forming a smoother, more refined surface on the final casting, sharp edges and finer patterns, improving the overall aesthetic quality of the casting.
Resin Sand Casting: Best surface finish; surface roughness ranges from 3.2 μm Ra to 12.5 μm Ra (12.5 μm Rz to 50 μm Rz).
Vertical Sand Molding: High-quality finish and consistent quality; surface roughness ranges from 6.3 μm Ra to 12.5 μm Ra (25 μm Rz to 50 μm Rz).
Lost Foam Sand Casting: Good finish; variability based on pattern quality; roughness ranges from 6.3 μm Ra to 25 μm Ra(25 μm Rz to 100 μm Rz).
Green Sand Casting: Good finish but may require machining for critical surfaces; roughness ranges from 12.5 μm Ra to 100 μm Ra.
Resin Sand Casting: Best surface finish; surface roughness ranges from 3.2 μm Ra to 12.5 μm Ra (12.5 μm Rz to 50 μm Rz).
Vertical Sand Molding: High-quality finish and consistent quality; surface roughness ranges from 6.3 μm Ra to 12.5 μm Ra (25 μm Rz to 50 μm Rz).
Lost Foam Sand Casting: Good finish; variability based on pattern quality; roughness ranges from 6.3 μm Ra to 25 μm Ra(25 μm Rz to 100 μm Rz).
Green Sand Casting: Good finish but may require machining for critical surfaces; roughness ranges from 12.5 μm Ra to 100 μm Ra.
2.2. Production Cost(Lowest to Highest)
Green Sand Casting: Lowest cost due to simple materials and processes.
Vertical Sand Molding: Moderate cost, efficient for high volumes.
Resin Sand Casting: Moderate to high due to resin use.
Lost Foam Sand Casting: Higher cost due to process complexity.
Coated Sand Casting: Highest cost from precision requirements and materials.
Vertical Sand Molding: Moderate cost, efficient for high volumes.
Resin Sand Casting: Moderate to high due to resin use.
Lost Foam Sand Casting: Higher cost due to process complexity.
Coated Sand Casting: Highest cost from precision requirements and materials.
2.3. Tolerances(Highest to Lowest)
Resin Sand Casting: Offers tight tolerances, making it ideal for precision components. DCT4 ~ DCT7, GCT3 ~ GCT5
Coated Sand Casting: Provides good to tight tolerances, suitable for applications requiring high dimensional accuracy. DCT7 ~ DCT9, GCT4 ~ GCT7
Lost Foam Sand Casting: Achieves moderate to tight tolerances, though variability can occur based on pattern quality. DCT9 ~ DCT13, GCT5 ~ GCT8
Vertical Sand Molding: Delivers reasonable tolerances, with consistency aided by automation.CT9 ~ CT13, GCT5 ~ GCT8
Green Sand Casting: Generally offers the lowest tolerances among these methods, often requiring additional machining for critical dimensions. DCT10 ~ DCT13, GCT6 ~ GCT8
Coated Sand Casting: Provides good to tight tolerances, suitable for applications requiring high dimensional accuracy. DCT7 ~ DCT9, GCT4 ~ GCT7
Lost Foam Sand Casting: Achieves moderate to tight tolerances, though variability can occur based on pattern quality. DCT9 ~ DCT13, GCT5 ~ GCT8
Vertical Sand Molding: Delivers reasonable tolerances, with consistency aided by automation.CT9 ~ CT13, GCT5 ~ GCT8
Green Sand Casting: Generally offers the lowest tolerances among these methods, often requiring additional machining for critical dimensions. DCT10 ~ DCT13, GCT6 ~ GCT8
Choosing the best sand casting method for gray and ductile iron involves balancing surface quality, production costs, and tolerance. Whether you need the superior finishes of Coated Sand Casting, the precision of Resin Sand Casting, or the economy of Green Sand Casting, we have the right solution for you.
Contact us at Shata Castings today to discuss your casting needs and let us help you achieve your project goals!
Blog
Contact Us
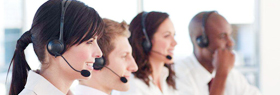
E-mail: [email protected]
WeChat: 18332109035
Whatsapp: 18332109035
Add: Shi Jiazhuang, He Bei Province