Products >> Aluminium >>
Bases/ Mount brackets
Choosing the right casting method for cast aluminium bases and mount brackets is crucial for performance and cost efficiency.
This guide outlines four main methods: die casting, gravity casting, low pressure casting, and sand casting, along with key considerations for each.
Key Considerations
1. Production Volume
- High Volume: Use die casting for large quantities due to its speed and efficiency.
- Low to Medium Volume: Opt for sand or gravity casting for smaller runs.
2. Design Complexity
- Intricate Designs: Die casting is best for complex shapes with tight tolerances.
- Simple Designs: Gravity and sand casting work well for straightforward designs.
3. Surface Finish
- High Quality: Die casting delivers excellent finishes with minimal machining.
- Moderate Quality: Gravity casting provides good finishes, while sand casting may need additional work.
4. Mechanical Properties
- Strength: Low pressure casting enhances strength and reduces defects.
- Weight: All methods can minimize weight, but material thickness must meet application needs.
5. Cost
- Budget-Friendly: Sand casting is cost-effective for low runs. Die casting has higher initial costs but lower per-unit costs in large volumes.
Casting Methods
1. Die Casting
- Process: Inject molten aluminium into steel molds under high pressure.
- Advantages: High precision and fast production.
- Uses: Best for detailed components like lighting fixtures.
2. Gravity Casting (Permanent Mold Casting)
- Process: Pour molten aluminium into preheated metal molds using gravity.
- Advantages: Good surface finish and dimensional accuracy.
- Uses: Suitable for larger parts, like machinery bases.
3. Low Pressure Casting
- Process: Push molten aluminium into molds using low pressure.
- Advantages: Better mechanical properties and fewer defects.
- Uses: Common in automotive and aerospace applications.
4. Sand Casting
- Process: Create a sand mold around a pattern, then fill it with molten aluminium.
- Advantages: Versatile and cost-effective for low to medium production runs.
- Uses: Ideal for custom parts and outdoor furniture.
Selecting the right casting method for aluminium bases and mount brackets depends on production volume, design complexity, surface finish, mechanical properties, and cost. Making an informed choice ensures high-quality components that meet industry demands. Ready to discuss your casting needs? Our team of experts is here to help you choose the right casting method for your project.
Get in touch here!
Products Category
Contact Us
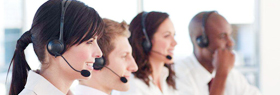
E-mail: [email protected]
WeChat: 18332109035
Whatsapp: 18332109035
Add: Shi Jiazhuang, He Bei Province